水プラズマ溶射
水プラズマ溶射装置はカーボン電極と鉄製回転陽極の間に水が流れる構造になっており、水(水蒸気)に電圧をかけることで高速のプラズマジェット炎を発生させ、粉末材料を溶融し、吹き付けます。
プラズマジェット炎の温度が最高30,000℃にも及び、単位時間当たり最大20kgと、材料処理量を他の溶射法と比較して大幅に上げることができます。
また、粒径の大きな材料を溶かし、気孔の多い粗な皮膜を成膜する特徴があり、数十ミリオーダーに及ぶセラミックの厚膜を形成させる能力があることから、国内唯一の大型セラミック成型品(ワプロック)の製造が可能です。
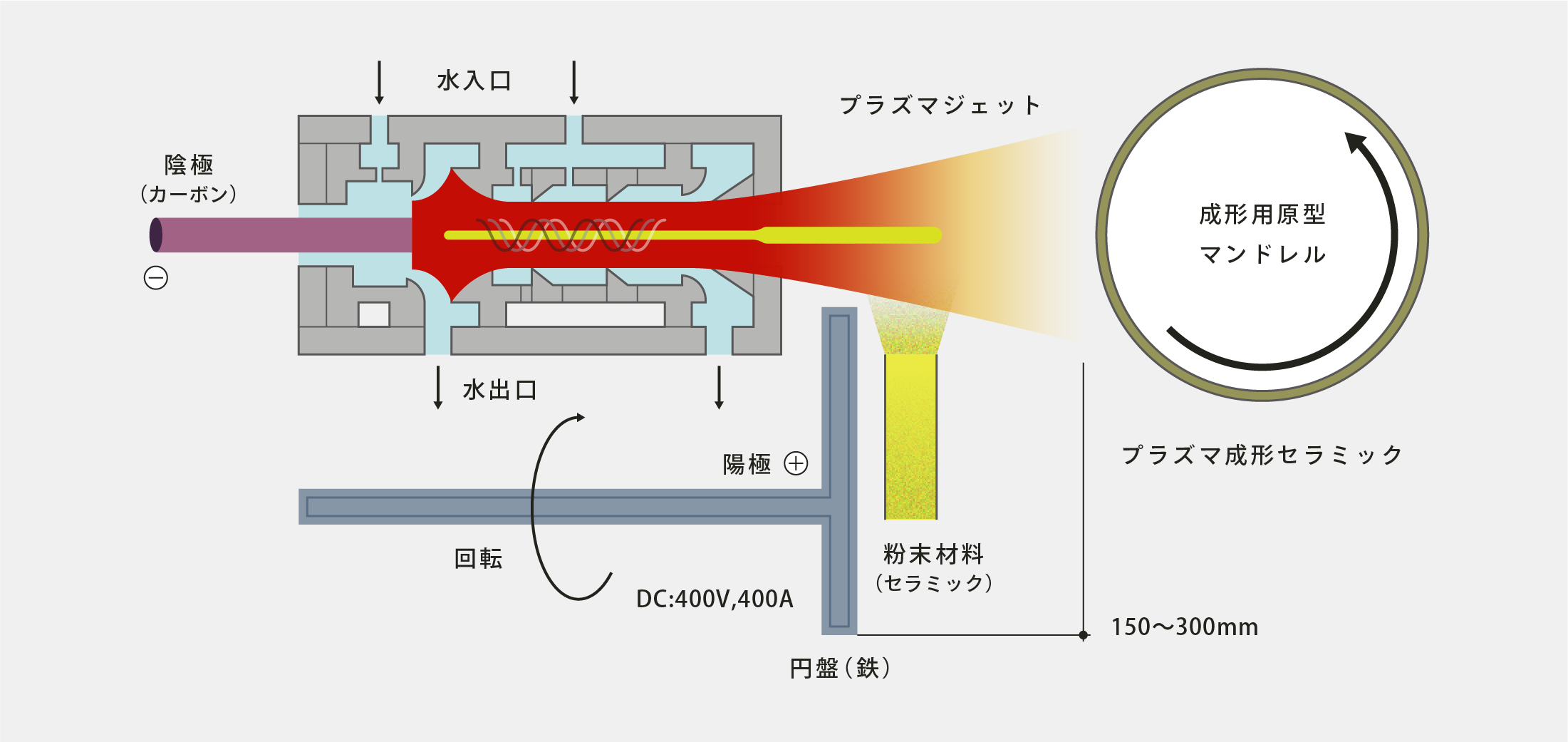
ガスプラズマ溶射
ガスプラズマ溶射装置はタングステン陰極と銅ノズル陽極の間にアルゴンやヘリウムなどの作動ガスが流れる構造になっており、そこに電圧をかけることでプラズマジェット炎が発生する仕組みになっています。
装置内で発生したプラズマは冷却ノズルの効果で通電領域の集中が起こり、15,000℃もの高温を生じさせます。
これにより金属粉末材料をはじめ、高融点のセラミック粉末材料が溶射可能です。
小型から大型製品と幅広い製品へ溶射ができ、また可搬式装置を所有しているため現地工事への適用も可能です。
より緻密で高品質な溶射皮膜を形成するため、特に耐熱・耐化学腐食に有効です。

高速フレーム溶射
燃焼室で液体燃料または燃焼ガスを純酸素と混合、燃焼させ、長さのあるノズルを通すことで燃焼ガスを加速膨張させることにより、高温超高速のガスジェットを発生させられる特徴があります。
ガスジェットの流速は音速の5倍にもなり、ガス流に乗せられた粉末材料は超音速に加速、製品へ叩きつけられるため非常に緻密で密着力の大きい高品質な皮膜の形成が可能です。
超硬合金とされるWC系やCrC系のサーメット材の溶射が可能で、鏡面仕上げに適した皮膜を形成するための条件コントロールが可能です。
また可搬式装置を所有しているため現地工事への適用も可能です。

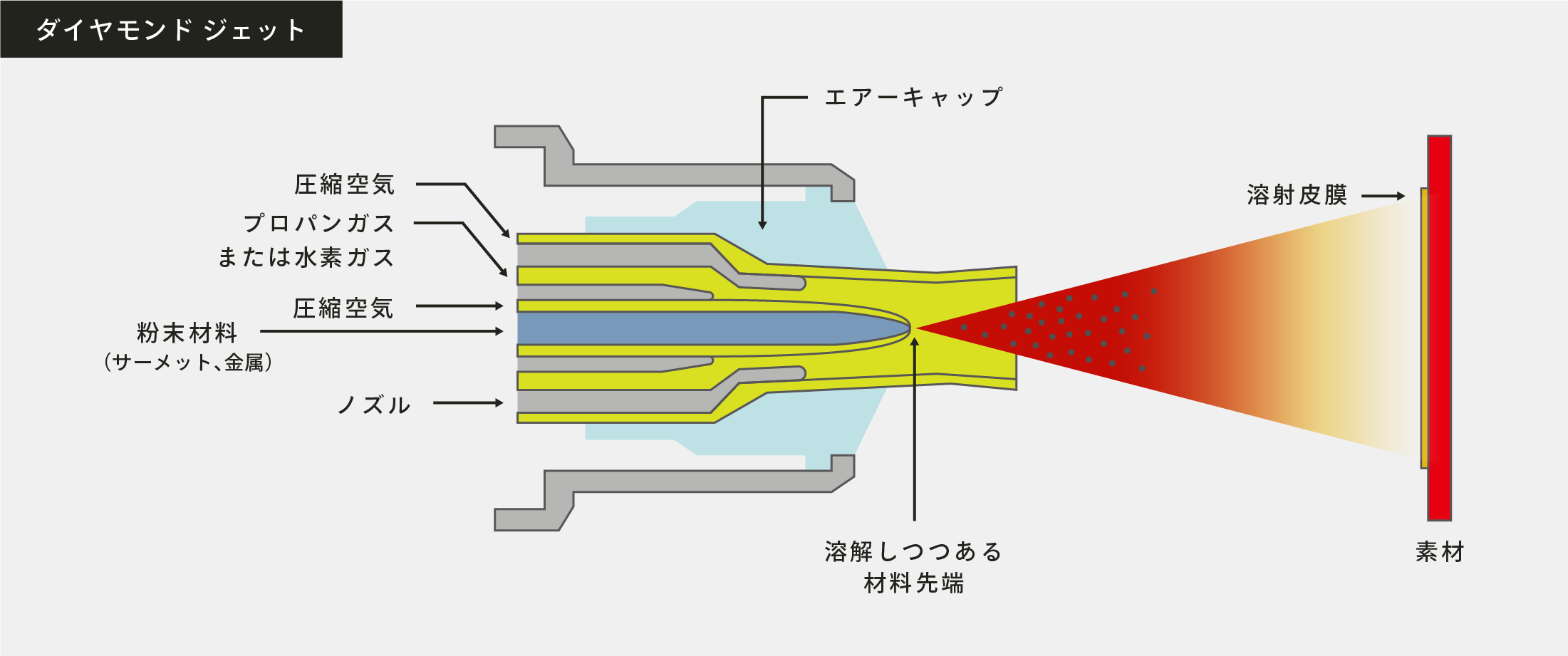
粉末式・
溶線式フレーム溶射
炭化水素系ガスと純酸素を混合して燃焼させることで生じた高温のガスに材料を投入し、材料を溶融、吹き付ける技術です。大阪富士工業のフレーム溶射で使用する材料は大きくワイヤ材料と粉末材料の2つに分けられます。
ワイヤ材料を採用した場合では、主に防錆溶射に代表されるアルミ合金や亜鉛合金などを使用し、現地溶射工事の実績を多数有しています。
熱影響による母材の変質・変化が少なく、材料選定においては他にロッドやチューブ形状での溶射も可能です。
粉末材料を採用した場合では、幅広い溶射材料を適用することが可能で、特にNi基やCo基の自溶合金の溶射が代表的です。
自溶合金は原料の付着効率が高く、再溶融処理により皮膜と母材が冶金結合するため、高密着力かつ貫通気孔のない溶射皮膜を形成することができます。
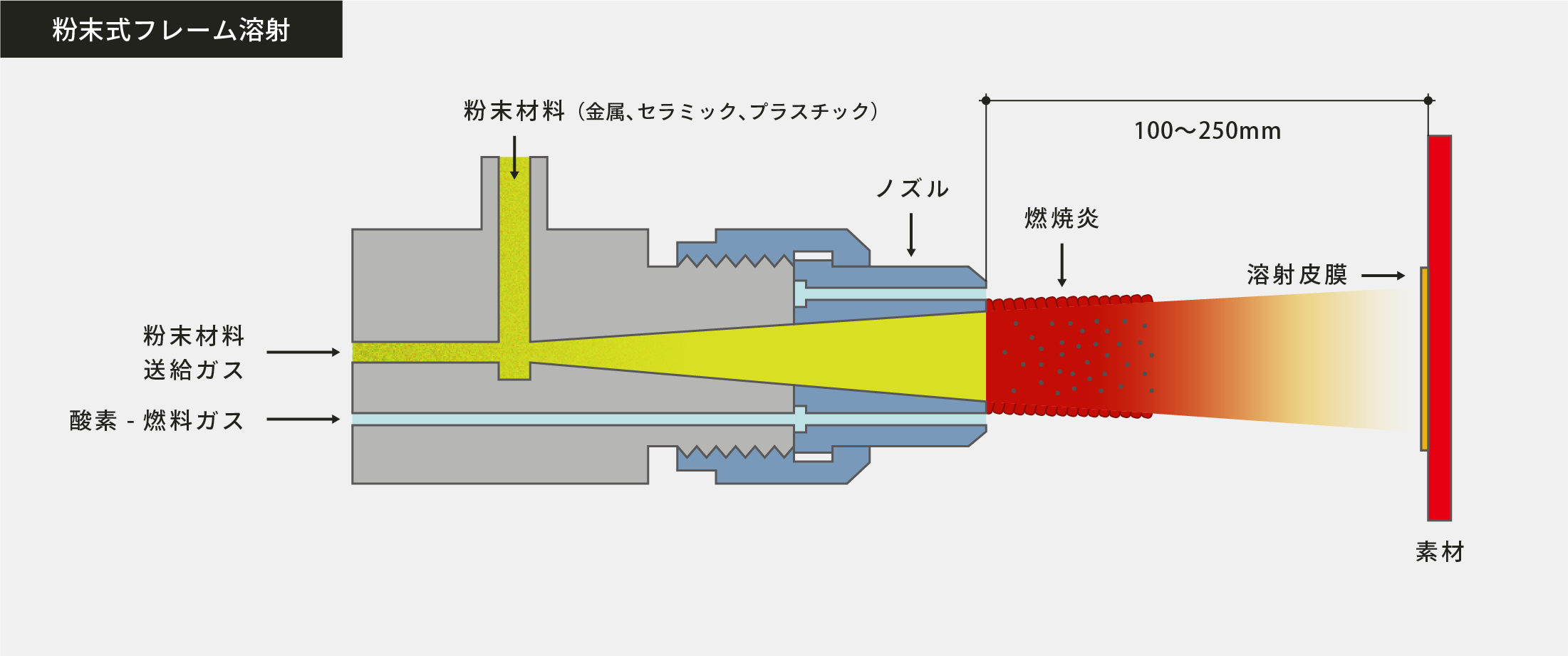
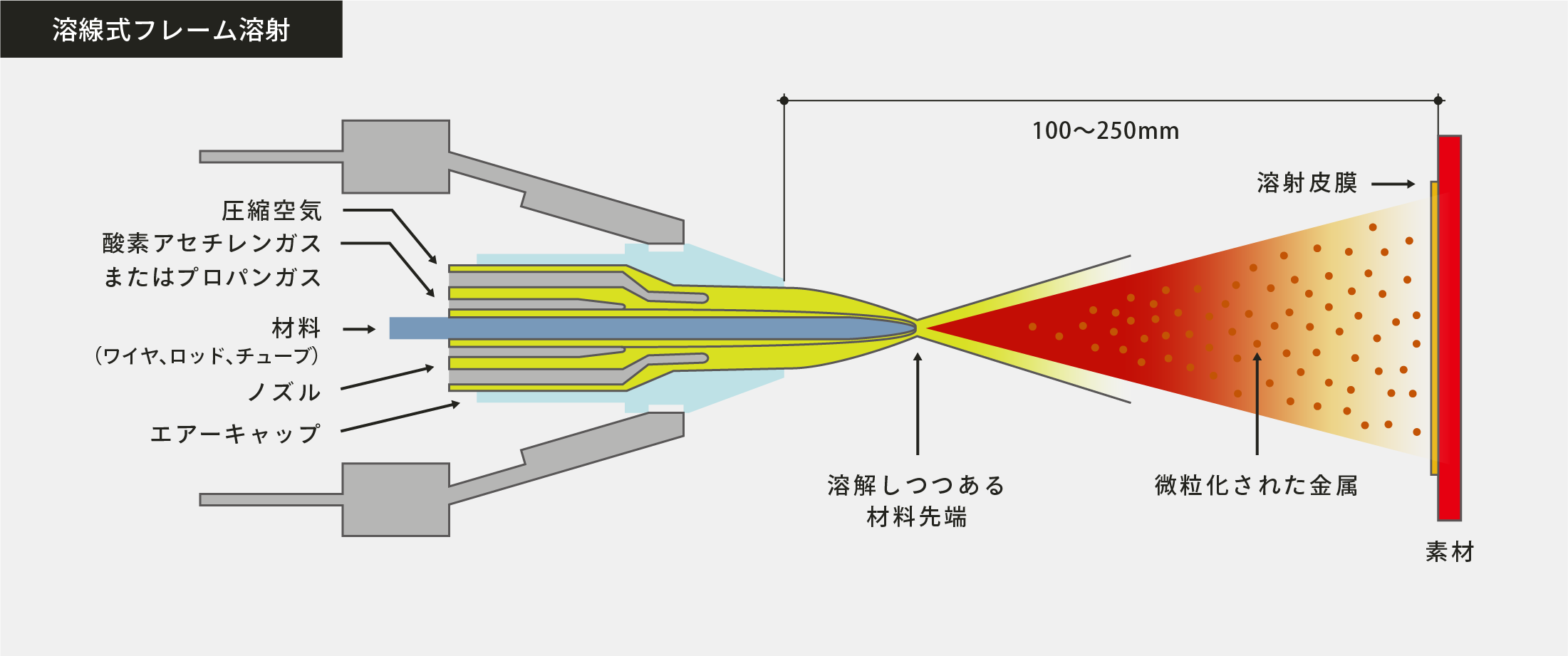
アーク溶射
プラスとマイナスに印加した2本のワイヤ材料をスパークさせ、6,000℃にも上る高温の材料液滴を生じさせた後、後方から高圧エアーを吹き当てて溶けた材料を加速、吹き付ける技術です。
皮膜形成速度が早く、密着強度・皮膜強度が高い、また混合材料や擬似合金化した皮膜を得られます。
20mmまでの厚肉盛溶射が可能で、現地での溶射工事にも適用されます。
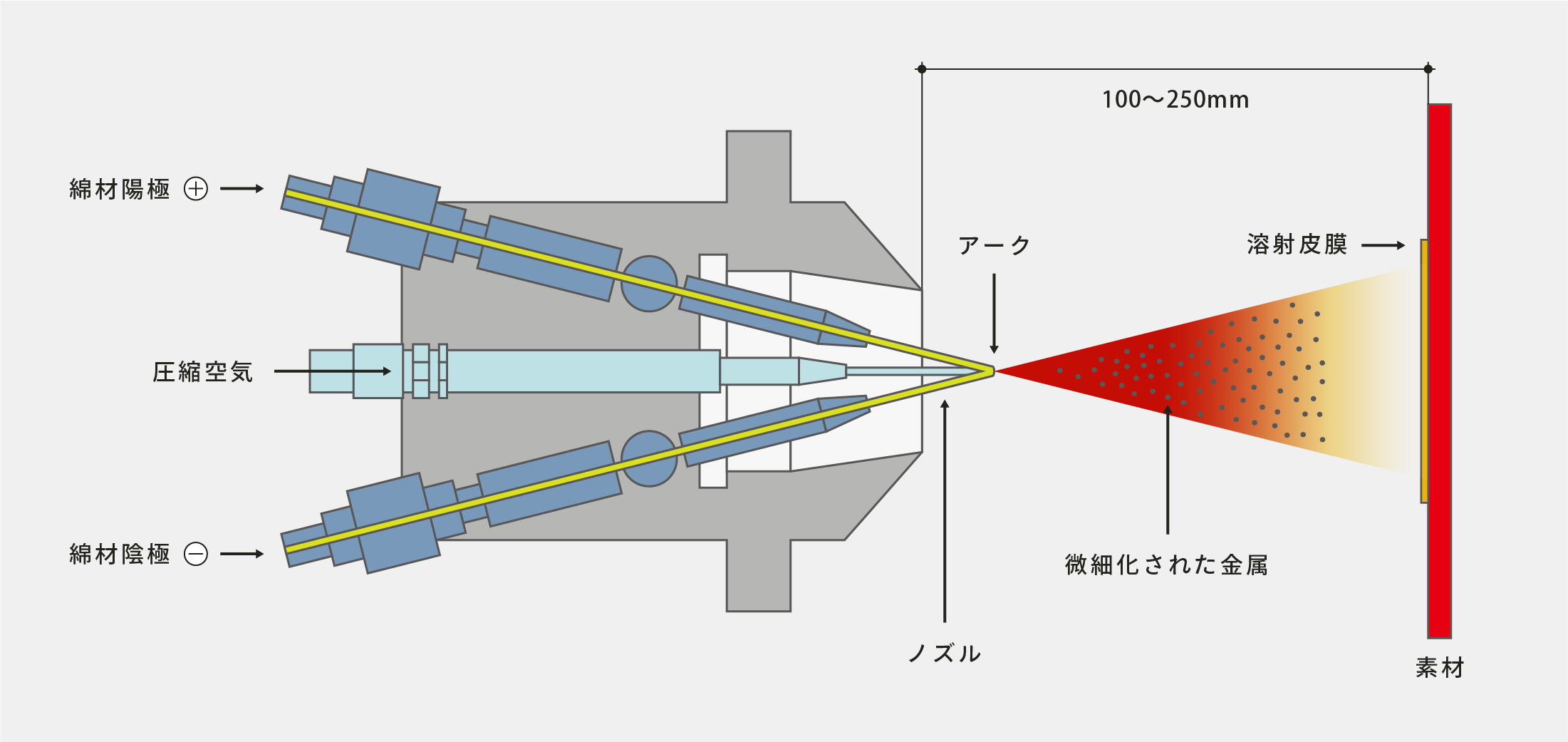